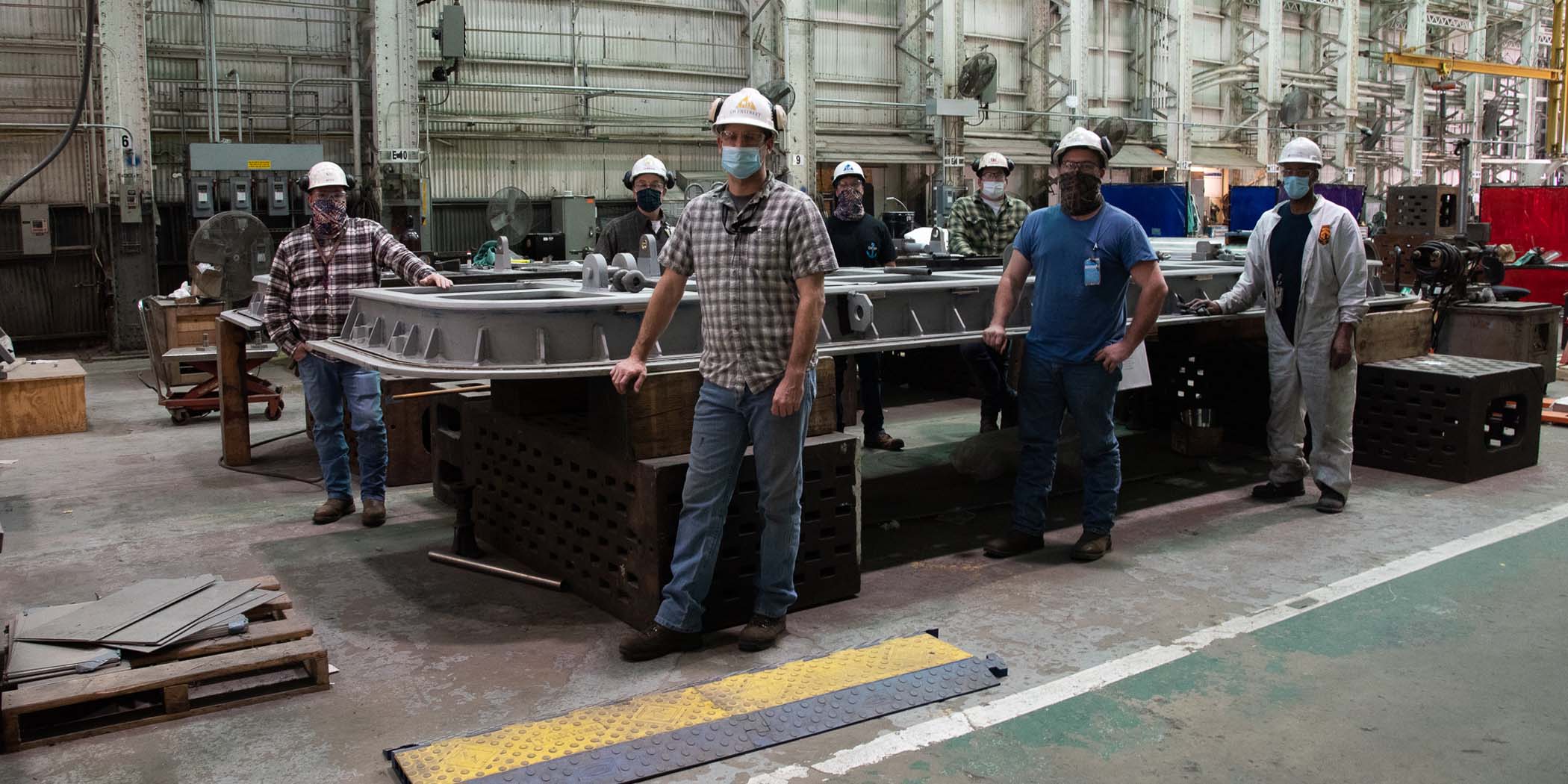
CVN 79 Team Makes Process Improvement
Published May 25, 2021
Shipbuilders working to install flight deck hatch doors for John F. Kennedy’s (CVN 79) advanced weapons elevators are grateful for a new process improvement that makes their jobs safer and more efficient.
In the past, Newport News Shipbuilding’s Machine Shop fabricated each hatch assembly upside down – which makes it easier to work the components that go underneath the hatch. Then, the hatch covers were assembled together. Once the assembly was ready for the ship, the hatch covers were disassembled and transported individually.
On CVN 79, shipbuilders would then work to reassemble the hatch covers, but in a less ideal position. “We’re working on the hatch with it flipped in ship’s position, not upside down. So now were crawling underneath it instead of working it on top,” said Nick Carter (X11), who specializes in weapons elevator hatches.
Because of tight tolerances and other variables the ship introduces, shipbuilders had difficulties replicating the results from the Machine Shop. Once the hatches were assembled, strongbacks were welded across the hatch covers to hold everything in place as they were lifted into elevator trunks.
Shipbuilders involved in the process saw an opportunity for improvement.
“Knowing the capabilities of the shop and going down to the waterfront and seeing their struggles and challenges, it just made sense for us to have the Machine Shop weld these together as an assembly before they ship them,” said Bubba Renn (X01), a construction supervisor who spent years working in the Machine Shop before taking on his current role. “It’s going to save us two or three weeks of trying to get everything lined up.”
M53 General Foreman Eric Nobles said the Machine Shop was open to the improvement idea. He said the shop would disassemble the hatch covers before shipping to allow for plates to be welded to them. However, that process has now been modified.
Each assembled hatch weighs about 20,000 pounds. Each of the ship’s four weapons elevators has two hatches that will help sailors move ordnance to the flight deck. Shipbuilders are looking forward to carrying the new process forward on Enterprise (CVN 80) and Doris Miller (CVN 81).
“It’s a lot better process,” said Sean Vanhorn, an X43 makeup foreman.