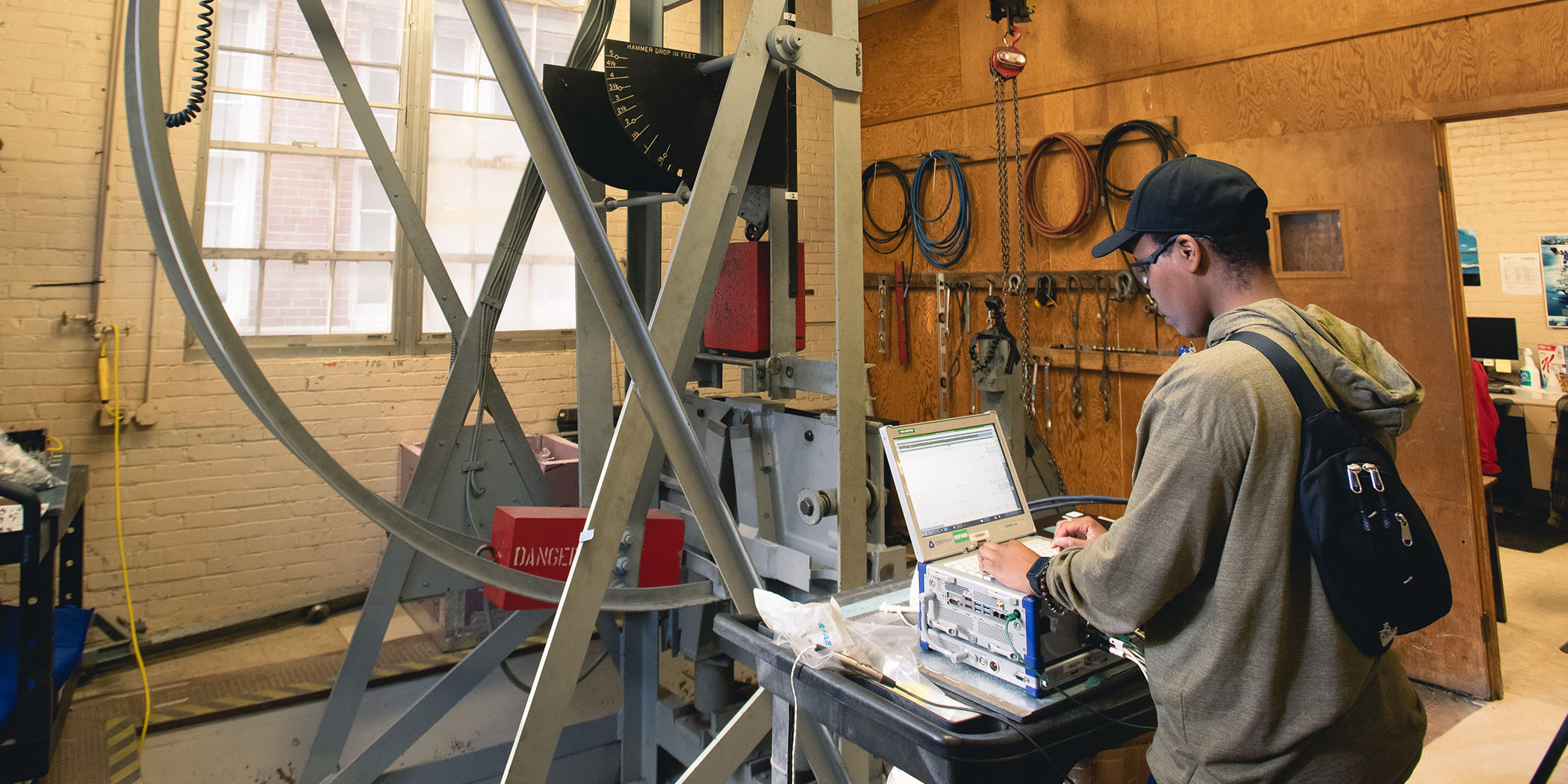
Put to the Test
Published July 7, 2021
Quality is continuously tested across Newport News Shipbuilding, especially in the shock test laboratory. It’s where engineers from different divisions test the durability of lightweight ship parts made by NNS and outside vendors.
“Engineers in the company come to us with a ship part and procedure describing what they want to test,” said Dave Conley, a material process engineer and manager. “We develop detailed test plans, take the part to the shock test room, physically test it, and write a report to document our findings.”
The team recently evaluated a circuit breaker housed within an enclosure – a part identical to those on aircraft carrier USS Gerald R. Ford (CVN 78).
“It’s important to test these products in the yard because you don’t want them to fail at sea,” said Melissa Vixama, an engineer in test program support. “It would be a lot harder to fix it out there and it could compromise the safety of individuals on the ship.”
Shipbuilders mounted the circuit breaker onto an anvil, which is a block of metal connected to the shock test machine. “Once mounted onto the shock test machine, we were able to strike the anvil with a large hammer weight that we released at different elevations,” said Rance Maruszewski, a material process engineer. “The shock test not only involves determining if the item can survive physically, but operationally.”
NNS’ data acquisition team monitored voltage levels at high sampling speeds to ensure the breaker didn’t trip during impact. “A successful test is if the breaker keeps a steady rate,” Vixama said. “It’s really cool. This is my first lightweight shock test and I’m learning a lot.”
After completed shock tests, reports are sent to the Navy for final approval.