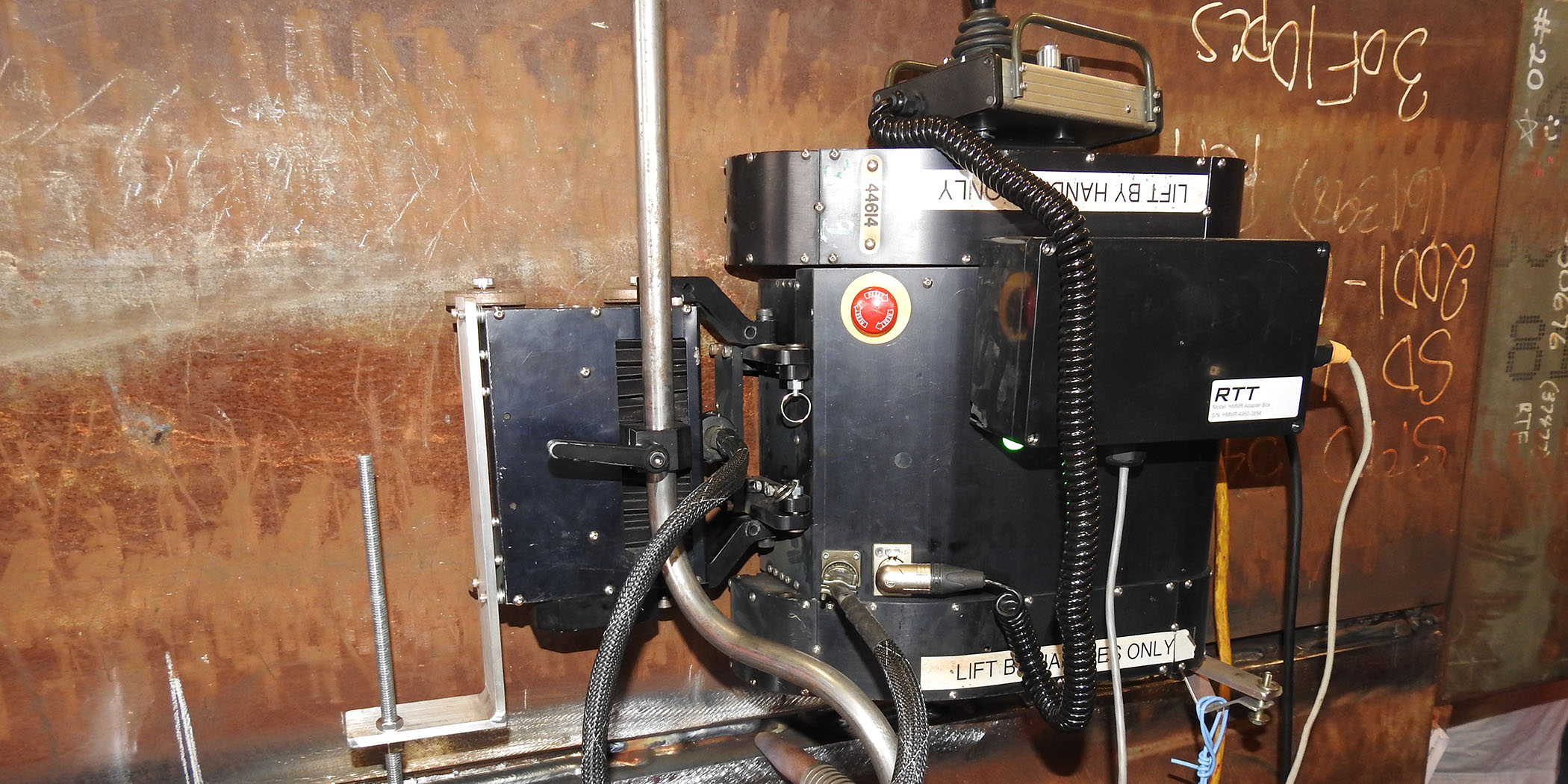
The Future of Welding
Published November 30, 2021
Heeding the call of “arc on,” observers’ welding helmets quickly come down. At the flick of a switch, a magnetic crawler begins to move, assisting the weld torch along its remotely controlled journey, filling the weld groove one pass at a time.
Welding – the process of joining two components together – is part art and part science. Working with molten filler metal is a potentially dangerous, labor intensive and critical tool in manufacturing environments. However, creation of this weld was far from typical; the magnetic crawler and weld torch are not manually operated by a welder or with a pendant, but rather through a haptic stylus and computer, feet away from hot steel. Peering intently into a laptop, a welder skillfully completed his first Tele-Weld pass.
The overall project was facilitated by Newport News Shipbuilding Technology Development (E32). NNS is the lead partner along with the Edison Welding Institute for Tele-Welding: Remote Operation of Shipyard Welding Equipment project. Further support came from the National Shipbuilding Research Program (NSRP), which aims to reduce total ownership cost and improve capabilities of both government and commercial ships.
Additional partners include Robotic Technologies of Tennessee, General Dynamics Electric Boat and Visible Welding. Three years in the making, the design impetus was to:
- Develop a system allowing craftsmen and craftswomen to operate welding equipment from a remote location.
- Create a method for craftsmen and craftswomen to get exposure, gain confidence and guide future efforts in remote controlled manufacturing technologies.
The system demonstrated is designed specifically for mechanized MIG welding. However, remote welding technology could be expanded to other types of welding in the future.
Remote welding is not a new concept for NNS. The company already has some welding set-ups for specific applications using cameras to view welds with a set work station distanced from where the weld is made. The main difference of the Tele-Weld system is its trackless crawler, which provides more versatile capabilities, and a portable remote system with potential to be located anywhere.
“The main impact to welding operations this technology would have is the ability to better utilize existing experienced welders who, due to age, injury, or other mobility restrictions, cannot weld in some of the more physically demanding shipyard environments,” said Ryan Lottes, project welding engineer. “It would also prevent injuries and provide a better work environment for trades currently welding applications where a Tele-Weld system could be used.”
The welding test group saw a great deal of promise in the remote Tele-Weld system and recognized benefits it could offer welding trades. As subject matter experts, welders provided valuable feedback to developers on additional capabilities the prototype system needs to be effectively used at NNS.
Implementation of this technology ultimately has potential to shift welding into a high tech, clean environment while encouraging a new generation to consider welding and manufacturing as a career choice. By significantly reducing geographical labor pool impacts, remote welding can allow personnel of diverse physical capabilities to contribute to the workforce.